Manufacturers Will Spend $26.2 Billion in 2020 To Train Employees & Keep Skilled Workers
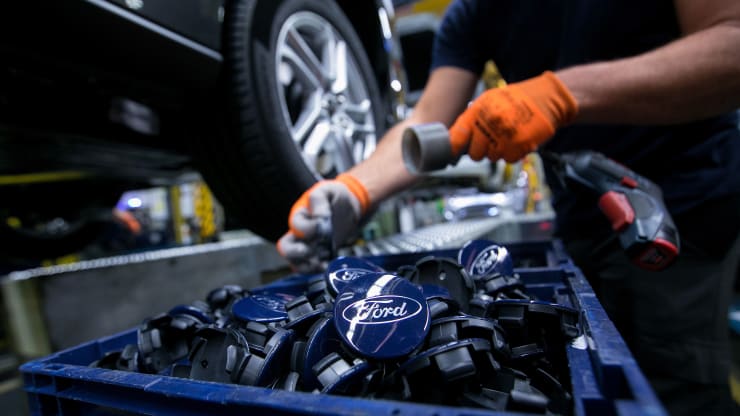
A worker puts the Ford logo on wheels in Germany
The amount of workers with little skills, or no skills in America is only getting worse, according to a new report by CNBC.
Companies are spending more to train their employees and current workforce to secure a future of skilled employees.
Manufacturers are expected to spend $26.2 billion on internal and external training initiatives for existing employees, and new employees. This training will help to fight the overwhelmingly number of skilled workers, the Manufacturing institute says.
With a skills gap hitting the heart of America manufacturing hard, companies are investing big to “upskill” their current workforce.
Almost 70% of manufacturers said they are creating or expanding training programs for their workforce. The study also showed that three quarters of the responses were that upskilling workers helped to improve productivity, promotion opportunities, and morale.
The Skilled Worker Gap Grows
The skill gap has been the number 1 challenge for manufacturers for the past three years, according to the National Association of Manufacturers Outlook Survey, which found that the inability to attract and retain the best workers has been a top concern.
In the third quarter of 2019 nearly 80% of respondents said they are struggling to find talent to fill open job positions. This lack of available workers has also made one third of companies turn down business opportunities.
Securing the future talent is a key priority for success. 4.6 million workers will be needed in the manufacturing sector by 2028, but 2.4 million of those jobs could still be empty if the proper steps are not taken to train employees.
The new manufacturing jobs of 2020 are not like the old manufacturing jobs of the early 1950’s and 60s, they are more high-tech, clean, and can be compensated well for those who climb the ranks.
Custom label printing is a good example of this, in the past it use to be very messy and use dangerous chemicals, today custom label printing is much different more clean, and more safe because of technoloy.
Bay Tech Label Printing Training
At Bay Tech Label company we are always investing in our future, and employees. Because the custom labels printing industry is always changing with new materials, technology and equipment.
Here are the four different ways Bay Tech Label is investing in the future of the company, label printing, and it's emloyees.
1. FIRST Certification - Bay Tech is a FTA FIRST certified label printing facility, and trains employees for FTA (Flexographic Technical Association) certifications Level 1, 2 and 3.
These classes are known at the FIRST operator certification Level 1,2, and 3 and helps new employee's to learn the history of label printing, to the current day technology of printing custom labels.
"FIRST is a document created by industry professionals containing specifications and tolerances for flexography. To assist the flexographic workforce in complying with it, FTA developed FIRST Individual Certification programs and FIRST Company Certification." the official website says.
2. Materials Training - With vendors and suppliers like Avery Dennison and Fasson, Bay Tech Label is always keeping staff updated on the latest and greatest, this allows employees to stay up to date with the latest trends, materials and methods of printing labels and flexible packaging.
3. Xeikon Digital Label Printing Training - By bringing in digital label printing experts onsite, our press operators are trained from experienced digital label printers, which allows Bay Tech label to print high quality labels faster for our customers, and more efficiently.